New Developments in NIR
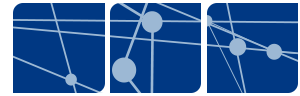
Breaking the mold and pushing the boundaries of NIR
Near-IR and Mid-IR, as technologies, have been around for decades. Certain applications for proximates testing and general identification have been well established for Infrared technology in the food, feed, and grain industries. Eurofins QTA challenges those boundaries by pushing Infrared into new material matrices and areas of quantitative analysis. One example is work done at a customer facility that works with Limestone and Quicklime.
One such customer is a large US based company that mines and processes limestone creating a series of quicklime products. They began working with Eurofins QTA to determine the calcium carbonate and magnesium carbonate concentrations in the limestone coming out of the mine. On the surface, no one would consider Limestone testing to be a wheelhouse IR application. However, through the use of targeted sampling, spiking, chemometric techniques, and the more traditional XRF data QTA was able to build algorithms and model groups to monitor the calcium carbonate concentrations (90-96%) in the outbound limestone. Furthermore, they were able to create NIR model groups to determine magnesium carbonate concentrations (2-7%), the major contaminant, as well as minor contaminants such as Aluminum Oxide (<1%), Iron Oxide (<1%), silicon dioxide (<1%), and potassium oxide (<1%).
Beyond the algorithm development, the Eurofins QTA team collaborated with an instrument manufacturer to create a system built to be installed directly over the conveyor belt and continuously take direct readings of the material moving by on its way out of the mine and to the kiln. This takes the customer from getting 1 data point every few hours from an XRF method on a small grab sample to continuous data points every 2 minutes where each data point is representative of almost 200 linear feet of material. NIR analysis enabled them to have a better perspective on all the material rather than chasing the noise of sample sizes that are way too small to be representative. This continuous data was the key to a massive improvement in their ability to achieve optimal material blends in their kiln for a more consistent finished product.
Eurofins QTA is now working with multiple locations for similar systems to analyze the raw limestone coming out of the mines and quarries as well as oxide and hydrate products.
This is just one example of how QTA enables producers and processors to harness the power of NIR out in production areas where they get the most value from continuous real-time data to make production decisions that directly impact their bottom line.